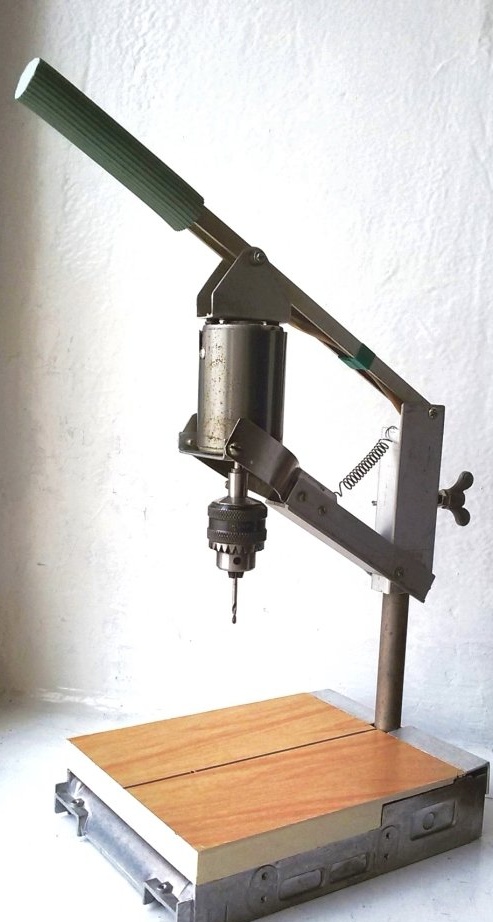
Se propune realizarea unei mașini de găurit mici, cu un design foarte simplu. Pentru fabricarea sa, nu vor fi necesare piese tip model - ghidaje precise, rulmenți, mecanisme de mișcare. Dacă în gospodăria dvs. există un motor cu instrument mic, cu mandrină de foraj pe arbore, atunci puteți începe să lucrați. Facem mașina din materiale improvizate. Billetele pentru componente nu vor fi greu de găsit.
Caracteristici de proiectare.
Această mașină este ușor de fabricat, dar are unele limitări. Designul său este proiectat pentru găuri de găuri până la 10 mm adâncime. Capacitățile mașinii în diametrul de foraj și materialul prelucrat depind de caracteristicile (puterea, viteza de rotație a arborelui) a motorului electric utilizat.
O limitare a adâncimii de foraj este asociată cu proiectarea suspensiei de antrenare. Dispozitivul se bazează pe un paralelogram cu balamale. Două paralelograme de legături verticale, egale în lungime și opuse, acesta este motorul electric și baza suspensiei. Celelalte două legături egale și opuse sunt elementele de legătură. După cum știți, în acest proiect, legăturile opuse vor fi paralele la orice rotație a legăturilor de paralelogramă. Prin urmare, axa comună a motorului electric și a burghiului (la fabricarea exactă a elementelor paralelogramei) va fi întotdeauna paralelă cu axa suportului fix și perpendiculară pe masa mașinii.
Pentru referință, un romboid este un paralelogram în care laturile adiacente au lungimi diferite și unghiurile nu sunt drepte.
Configurarea și funcționarea mașinii.
Poziția legăturilor de conectare paralele cu tabelul va fi luată ca poziția zero. Când prelucrați o piesă pe o mașină, pentru a crește precizia, locația acestor legături ar trebui să se apropie de o poziție orizontală.
În acest caz, cu mișcarea axială a burghiului de la +5 mm la -5 mm (cursă de 10 mm) din poziția zero a verigilor, decalarea radială a burghiului (în plan romboid) va fi de 0,08 mm. Această cantitate de deplasare va fi la o lungime de legătură de 150 mm. În practică, această deplasare este imperceptibilă și nu va fi critică pentru scula și gaura prelucrată.
La găurirea plăcilor de circuit imprimat, chiar și cu o unealtă din carbură fragilă cu un diametru de 0,8 mm, decalarea burghiei de pe placă cu o grosime de 2 mm va fi 0,003 mm (3 microni). Comparați valoarea dată cu compensarea și poziția acestui burghiu atunci când prelucrați plăcile manual.
Setarea mașinii la dimensiunea piesei, în înălțime, se realizează prin deplasarea rapidă de-a lungul suportului mașinii, a bazei suspensiei și fixarea acesteia cu un șurub deget mare. Înălțimea ridicării și fixării bazei suspensiei este determinată vizual de riscul poziției zero (reprezentat pe baza suspensiei - ultima fotografie) atunci când atingeți partea cu vârful burghiei. Când găuriți diferite plăci cu o grosime de 1 ... 3 mm, nu este necesară o reajustare în înălțime.
Avantaje suplimentare de proiectare.
Posibilitatea de a instala placi de dimensiuni mari (cu o creștere a înălțimii forajului, crește precizia forajului).
La eliberarea mânerului, la sfârșitul forajului, motorul cu un burghiu sub acțiunea arcului se ridică repede și înapoi o distanță considerabilă, eliberând zona de prelucrare a piesei.
În poziția cea mai înaltă, puteți schimba în mod convenabil rapid și sigur burghiul.
Cred că caracteristicile de mai sus vorbesc în favoarea fabricării mașinii propuse. Timpul petrecut la fabricarea acestui proiect de mașină plătește cu bună dispoziție de la excluderea defecțiunilor de exerciții scumpe și rare.
1. Materiale și detalii aplicabile.
Motor electric și mandrin mecanic sau cu colț.
Bucăți dintr-o foaie de metal cu grosimea de 1,5 ... 2,0 mm.
Închiriere profil din aluminiu, țeavă.
2. Realizarea unei mese a unei mașini de găurit.
În primul rând, trebuie să decideți cu privire la masa mașinii de găurit. Mărimea, rigiditatea și rezistența acestuia vor determina precizia și ușurința de utilizare. Există multe modele de mese diferite. În versiunea dată a aparatului, se folosește cazul CD player-ului, care aștepta de mult timp utilizarea sa secundară. Carcasă dreptunghiulară cu dimensiuni de 145 x 200 mm, turnată din aliaj de aluminiu. Are o greutate redusă, o structură rigidă și o planeitate de-a lungul periferiei părții inferioare a părții, ceea ce conferă o bună stabilitate produsului viitor. În plus, această parte nu necesită practic o prelucrare suplimentară. Din aceste motive, carcasa a fost luată ca bază a mesei pentru mașini.
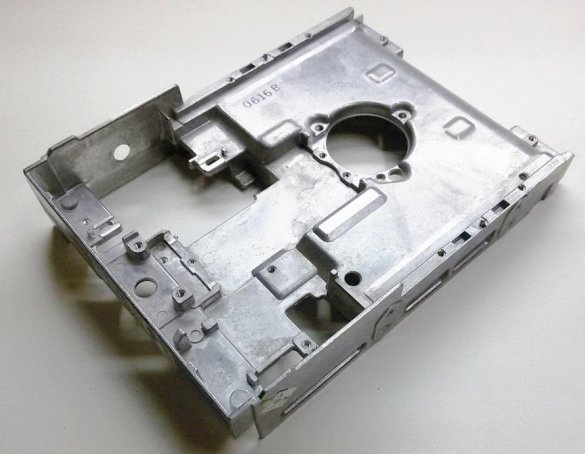
Unul dintre pereții scurti (în fotografia din stânga), în mijloc, are o gaură pentru șurubul M8, care determină automat instalarea suportului mașinii acolo.
Ca suport, puteți folosi metal laminat sau o țeavă cu un diametru de 18 ... 25 mm.
Structura analizată a folosit un tub de oțel cu pereți subțiri cu un diametru de 18 mm, ceea ce a făcut posibilă simplificarea metodei de fixare a acestuia pe masă.
Selectăm un șurub cu un fir M8 și un cap, al cărui diametru se potrivește strâns în orificiul din tub (poate necesita o rafinare a diametrului). Înșurubați piulița pe șurub și apăsați-le în tub. Standul este gata. Rămâne să-l fixați pe masă cu o a doua piuliță.
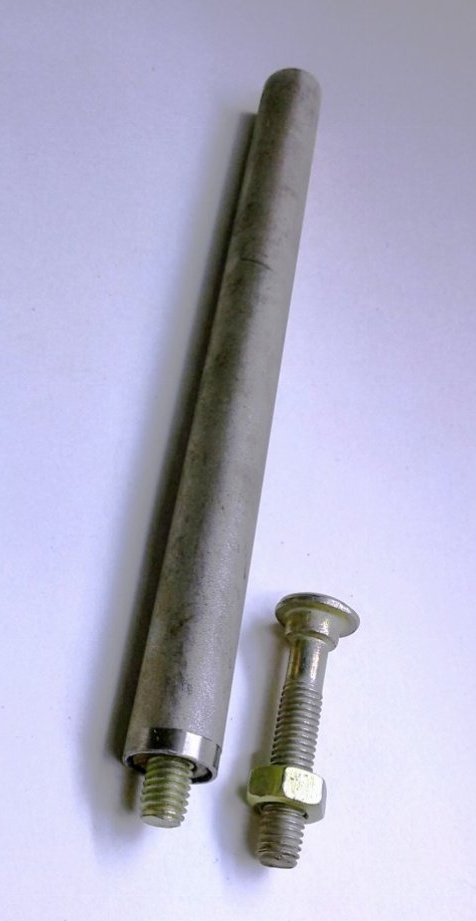
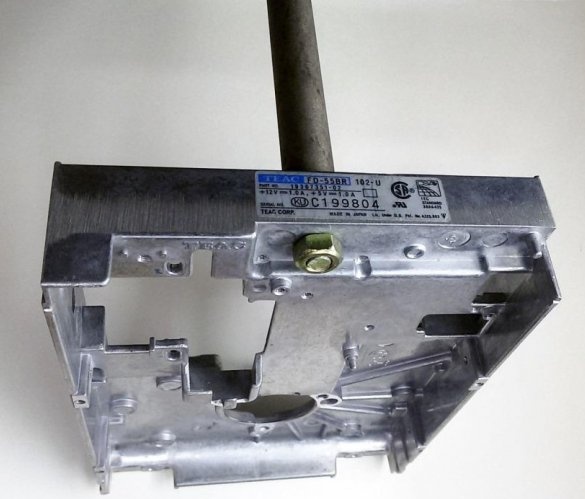
În partea superioară a mesei fixăm blatul tăiat din PAL laminat de-a lungul conturului corpului piesei de prelucrat. În acest caz, suportul pentru mașină va fi în plus, între peretele carcasei și blatul. În viitor, pe părțile libere ale suportului fixăm căptușeala unui pătrat din aluminiu. Toate acestea vor asigura rigidității suplimentare a suportului instalat.
În acest proces, verificăm și, dacă este necesar, reglăm perpendicularitatea suportului mașinii pe masă.
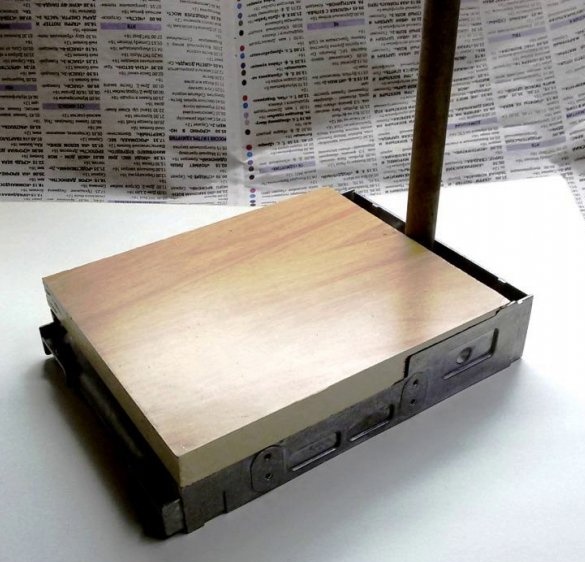
3. Realizarea bazei suspensiei.
Baza de suspensie este necesară pentru a instala mecanismul paralelogramului articulat pe suportul mașinii. Acesta servește ca o parte integrantă a romboidului, îl fixează pe suport, la înălțimea dorită și la un unghi selectat de la marginea mesei. Profilul din aluminiu în formă de formă (18 x 40 mm), care a servit anterior ca mâner de ușă pentru mobilă, a fost folosit ca un gol pentru baza suspensiei.
În mijlocul unei secțiuni a profilului, aproximativ două lungimi ale motorului electric, găurim o gaură și tăiem un fir M6 sau M8 sub șurubul de fixare. Verificăm fiabilitatea instalării bazei de suspensie pe suportul mașinii.
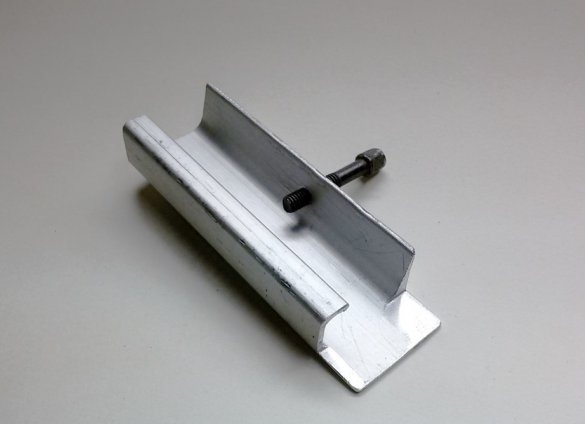
Fabricarea unui mecanism pentru montarea unui motor electric
4. Suport motor inferior.
Pentru mașina de găurit propusă a fost folosit un motor cu DC cu magneți permanenți DC 24V, 0,7A.
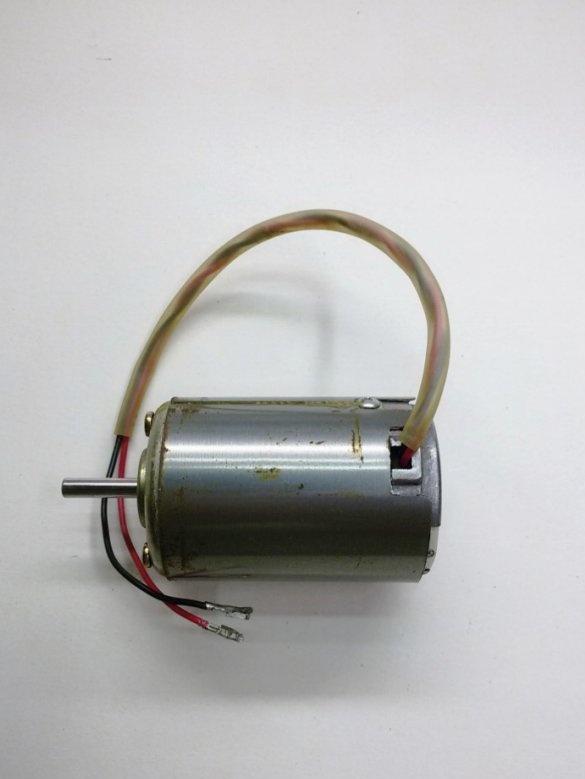
Începem producerea paralelogramului articulat cu veriga principală, formată dintr-un motor electric și elementele de fixare ale acestuia. Dimensiunile motorului utilizat pot fi diferite, precum și locația găurilor de montare. Prin urmare, dimensiunile elementelor de fixare nu sunt date.
Dintr-o tablă de oțel cu o grosime de 1,5 ... 2,0 mm, producem un suport motor inferior. În rafturile laterale ale suportului, găuriți găuri coaxiale și tăiați firul M4 în ele. Montați suportul motorului cu două șuruburi standard.
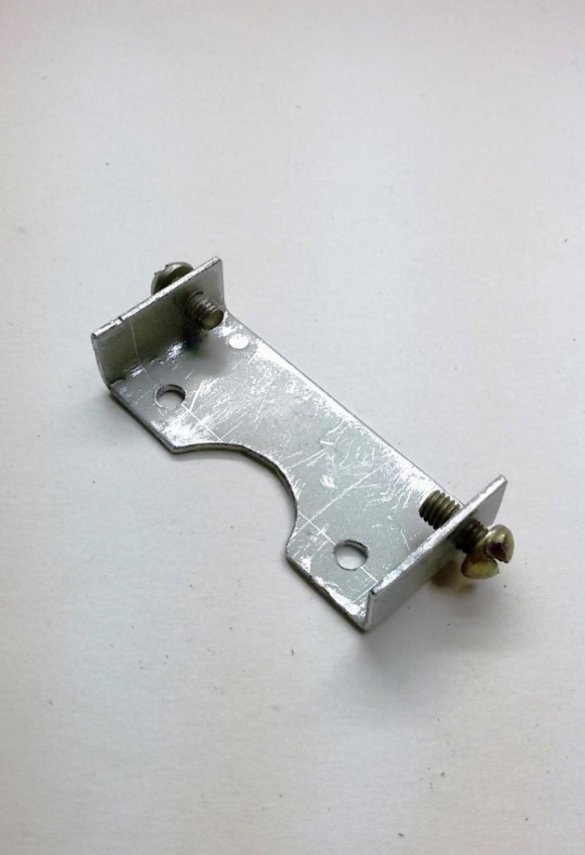
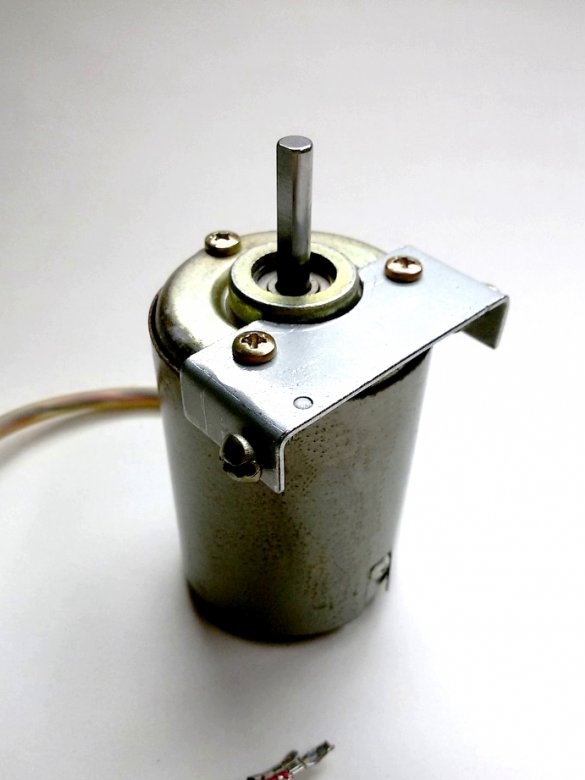
5. Legătura de jos a paralelogramei.
Vom face legătura inferioară a paralelogramei din aluminiu rulat disponibil la îndemână. De exemplu, în proiectul propus, a fost utilizat un profil de aluminiu în formă de U (20 x 20 mm), care a fost folosit anterior la fabricarea ferestrelor.
Pentru a conecta veriga inferioară cu suportul motorului, dintr-o foaie de oțel cu o grosime de 1,5 mm, producem două elemente de tranziție realizate în oglindă. Sunt conectate rigid la profilul de legătură cu două șuruburi (nituri).
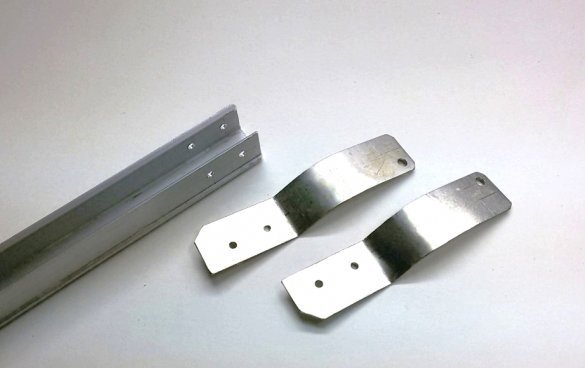
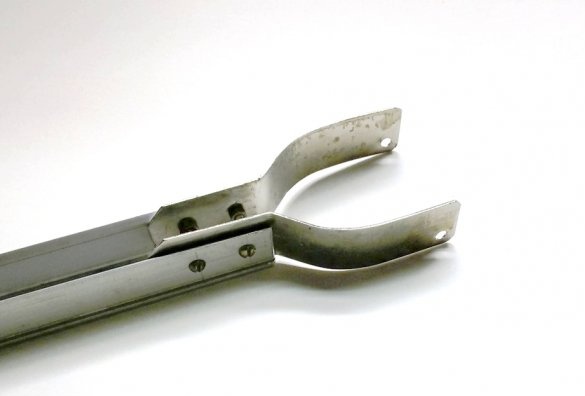
6. Legătură inferioară cu suport motor
Lungimea legăturii inferioare este determinată de mărimea tabelului fabricat. În acest proiect, această lungime (distanța dintre axele găurilor de montare) este definită drept 150 mm. Marcați găurile pentru conectarea la baza suspensiei și tăiați profilul la dimensiunea dorită. Dacă este necesar, pe partea tăiată a profilului, formăm lățimea canelurii pentru o legătură strânsă în lățime cu baza de împerechere a suspensiei. Foram de-a lungul găurilor coaxiale de marcare.
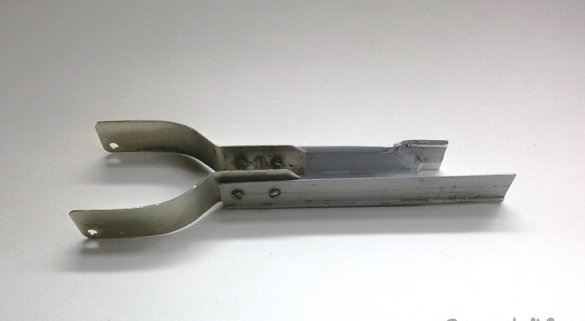
Asamblam legătura inferioară cu suportul motorului electric. Folosind șuruburile M4, atașăm veriga inferioară la suportul motorului, asigurând o rotație liberă în conexiune. Amplasarea orificiului de balamale din veriga inferioară, în spatele motorului, este determinată de creșterea maximă posibilă a lungimii verigii, prin urmare, creșterea preciziei prelucrării.
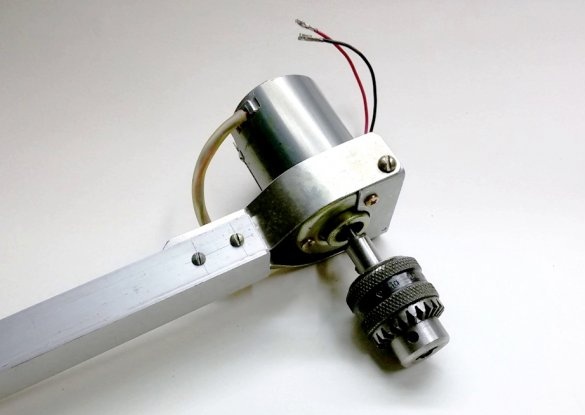
7. Suport motor superior.
Dintr-o foaie de oțel sau aluminiu cu o grosime de 1,5 ... 2,0 mm, producem suportul superior al motorului. Proiectarea piesei va depinde de locația punctelor de fixare pe motorul existent. Instalați suportul superior al motorului.

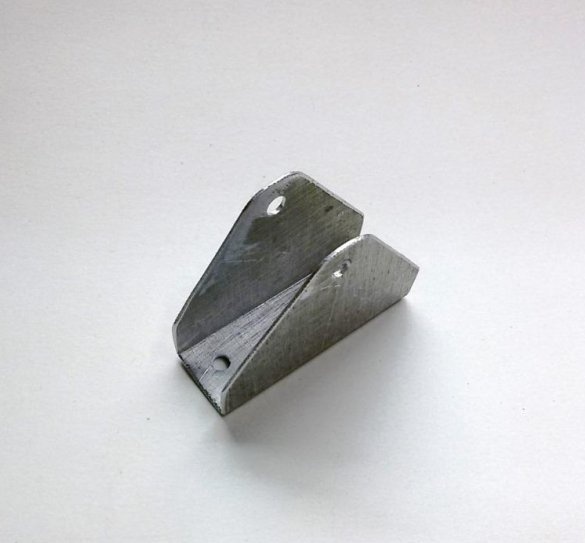
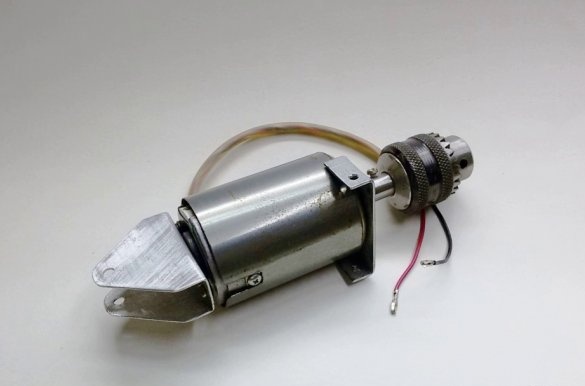
8. Legătura de sus a paralelogramei.
Legătura superioară a paralelogramei este, de asemenea, din aluminiu laminat. De exemplu, proiectul propus a folosit un profil de aluminiu în formă de H (12 x 16 mm). Marcați piesa de prelucrare a verigii superioare. Transferăm distanța dintre axele găurilor de montaj ale verigii inferioare fabricate pe piesa de prelucrat a verigii superioare. Găuri găuri pentru marcare. Lungimea piesei de prelucrare a verigii superioare, este de dorit să se dubleze, în raport cu dimensiunea de lucru a legăturii. Vom folosi capătul liber al profilului ca mâner pentru alimentarea burghiului, care va reduce forța mâinii la jumătate. O bucată de tub de plastic poate fi pusă pe această parte a piesei de prelucrat.
Distanța dintre axele orificiilor de montaj și locația lor pe suporturile motorului, ne transferăm la baza suspensiei. Cu alte cuvinte, în paralelogramul fabricat, liniile care leagă axele orificiilor de fixare de pe suporturile motorului și baza suspensiei trebuie să fie egale și paralele.
Pentru a îndeplini această condiție, în proiectarea mașinii fabricate, o parte din profil este decupată pe baza suspensiei (în partea superioară).
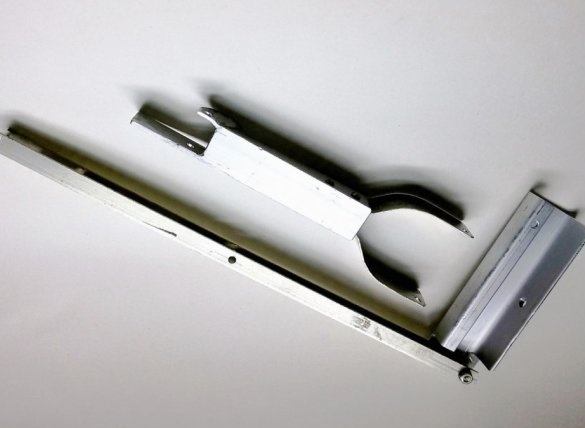
9. Asamblarea paralelogramei articulate - romboid.
Asamblăm un romboid, îl instalăm pe un suport și verificăm mecanismul în funcțiune.
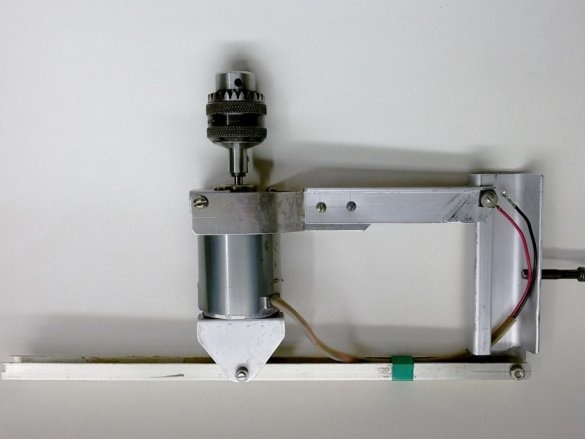

10. Controlul preciziei mecanismului
perpendicularității
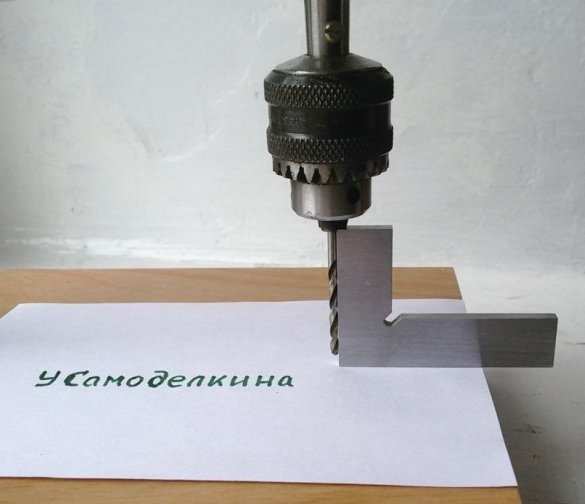
pentru exerciții cu o cursă de 10 mm
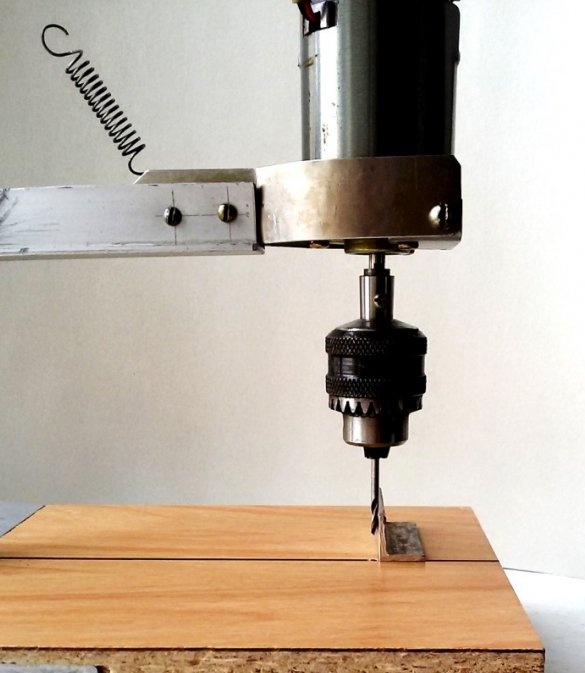
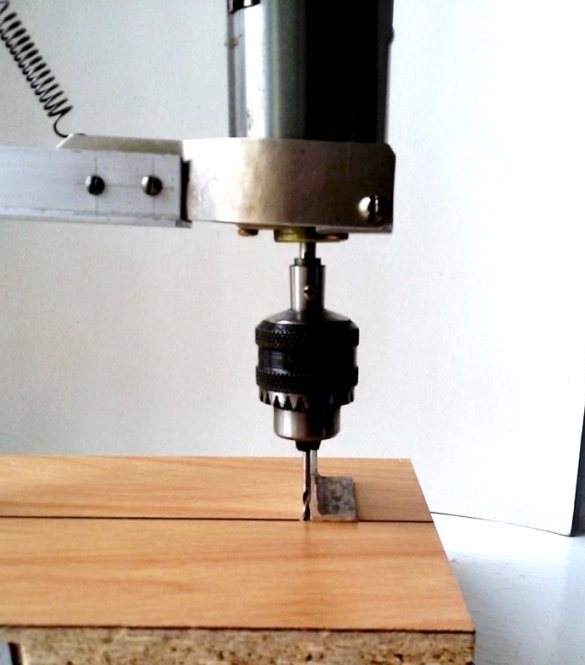
sub sarcină.
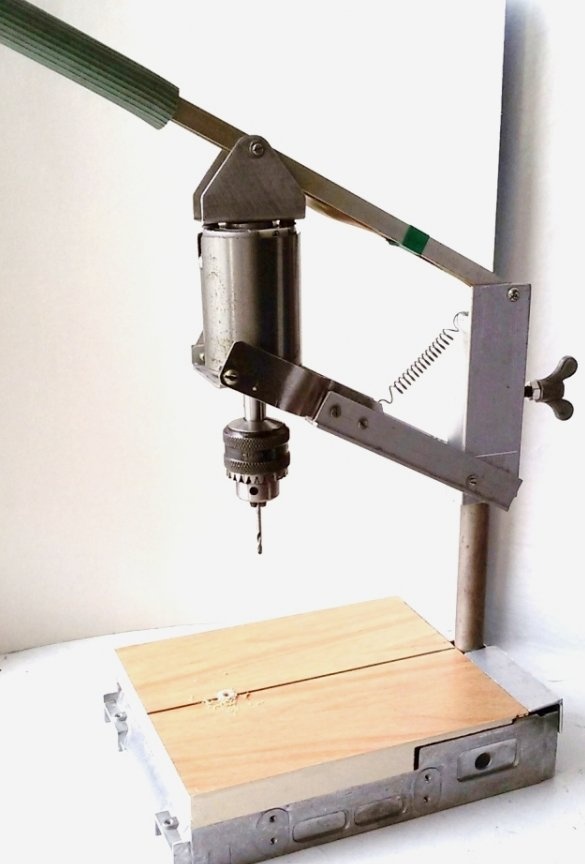