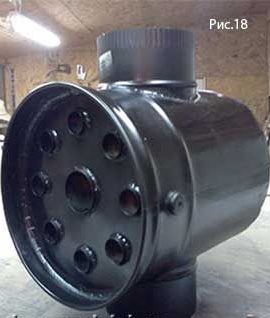
Multe persoane care au propriile lor ateliere, garaje sau doar case de țară, instalează acolo așa-numitele sobe. Această sobă a dobândit acest nume în 1917, în timpul revoluției. A primit-o pentru „glutonie” și nepretenție pentru materialele combustibile utilizate pentru cuptor. Acest cuptor câștigă, fără îndoială, simplitatea designului său, costul relativ redus, dar are un dezavantaj atât de serios, precum eficiența scăzută (eficiența), care este de aproximativ 15 - 20 la sută. De asemenea, pereții metalici nu foarte groși ai sobei acumulează slab căldură și atunci când arde combustibil, acesta se răcește destul de repede, deoarece căldura principală generată de aragaz doar zboară în conductă și „încălzește strada”. Pentru a crește eficiența, puteți mări suprafața suprafeței conductoare de căldură. Pentru aceasta este util un așa-numit schimbător de căldură. Este instalat în locul celei mai mari concentrații de căldură și poate crește semnificativ eficiența cuptorului.
Pentru a crea un schimbător de căldură veți avea nevoie de:
- O conductă cu un diametru de 32 mm, o lungime de aproximativ 2,5 metri;
- Țeavă 57 mm, lungime 300 mm;
- tabla de grosime de 1 mm, două pătrate de 350 mm fiecare;
- O găleată metalică de 20 litri;
- burghiu, polizor, mașină de sudat (de preferință semiautomatică);
Etapa 1. Producerea capacelor finale.
Pentru a face acest lucru, în pătratele de tablă, este marcată o gaură în centru. Din el este marcat un cerc cu o rază de 150 mm. Aceasta va fi raza sa exterioară. În continuare, centrul găurilor pentru conducta de 32 mm este marcat, pe o rază de 100 mm, și o distanță de 45 de grade între ele. Centrul foii este marcat sub o țeavă de 57 mm.
Pentru a găuri astfel de găuri, este necesar să găuriți un diametru mic pentru a găuri găuri (cu o marjă) în jurul circumferinței, a îndepărta mijlocul și a alezat la diametrul dorit cu un fișier.
Iată ce ar trebui să obțineți:
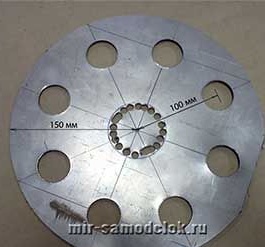
Pasul 2. Asamblarea țevilor și a dopurilor.
O țeavă de 32 de diametre este tăiată în 8 părți, fiecare având o lungime de 300 mm. Pentru a simplifica procesul de asamblare, folosim aici un astfel de șablon din placaj de 22 mm:
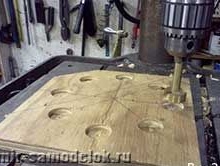
Apoi, țevile tăiate sunt introduse în șablon, se pune un capac și se prinde la 5-6 puncte. Complet scaldat va fi afară.
Ambele Stubs cad în loc:
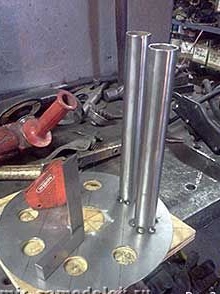
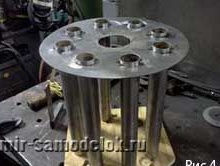
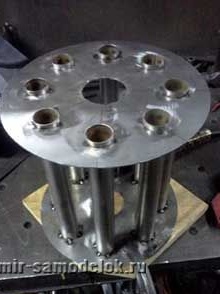
Cusătura trebuie să fie strânsă, astfel încât schimbătorul de căldură să nu se „eticheteze”:
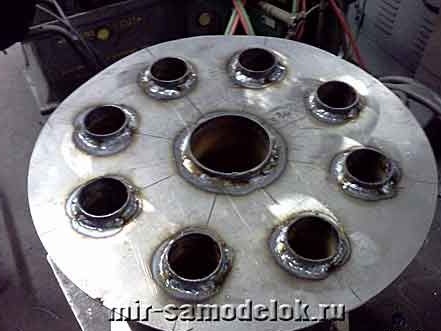
Etapa 3. Caz.
Carcasa este realizată dintr-o găleată rotundă de 20 de litri. Pentru a îndepărta vopseaua, este zguduită într-un foc.
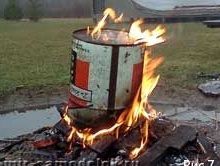
Acoperirea rămasă și funinginea trebuie îndepărtate cu o perie de sârmă. Partea inferioară a găleții este tăiată de o râșniță.
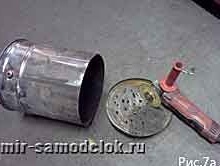
În continuare, trebuie să faceți două găuri la intrarea și la ieșirea conductei de fum. Diametrul lor este selectat în funcție de dimensiunea sa. În acest caz, a fost utilizată o țeavă standard cumpărată dintr-un magazin.
Iată procesul de construire:
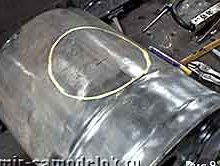
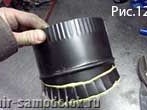
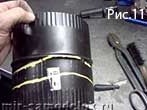
Mese crestături sunt făcute de-a lungul marginilor țevii și îndoite în partea interioară a corpului:

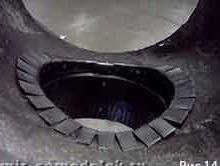
La exterior, țeava este ridicată de punctele:
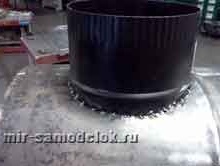
Deoarece grosimea metalului nu este suficientă pentru penetrarea completă, îmbinarea este sigilată cu un material de etanșare refractar:
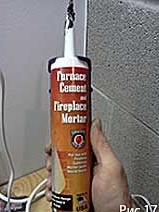
Pasul 4. Pictura.
Vopsirea se realizează cu vopsea refractară.
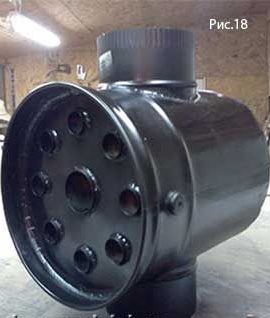
Pasul 5. Instalare.
Designul finalizat este instalat pe coșul de fum. Pentru a crește eficiența muncii sale, pe de o parte este instalat un ventilator care va arunca aer în schimbătorul de căldură. La ieșirea din ea, va fi mult mai cald. Ventilatorul trebuie instalat pe metal sau pe alte suporturi termorezistente.
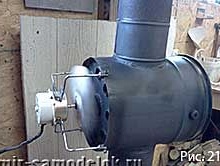
Concluzii.
După o astfel de perfecționare, timpul necesar pentru încălzirea completă a camerei a fost redus semnificativ. De asemenea, a scăzut consumul cuptorului.
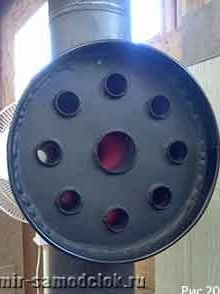
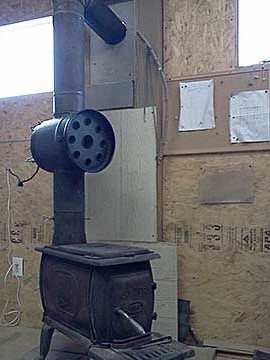